5 minutes with... Alan Thomas
Alan Thomas from ZwickRoell Limited.
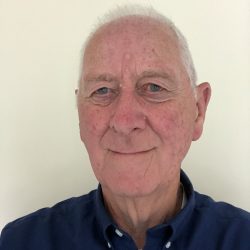
What is your role?
ZwickRoell is a leading global supplier of materials and component testing products. My role is to promote the ZwickRoell brand and mechanical testing solutions across the U.K. and Ireland. We offer a comprehensive range of advanced technology materials and component testing products to satisfy the needs of over 20 different industry sectors and academia. In an industrial setting, our equipment is employed in both research & development, production and quality assurance applications, whilst in academia it is used for both research and teaching purposes.
What are the biggest challenges in the industry at the moment?
One of our most important challenges is to ensure that our range of testing equipment always provides test results which are accurate, repeatable, reproducible and traceable. Our test results are transparent and traceable due to continuous documentation of machine data, test parameters and user information. We meet the strictest internationally recognised standards and guidelines for every test and guarantee the highest level of test result reliability.
It is important that we support our customers from every angle and that we are not only able to satisfy the widest range of test requirements, but that we support our customers throughout the entire life-cycle of the testing sytem with tailored support services which are available anywhere in the world. For our materials testing machines we guarantee the availability of spare parts for at least 10 years after a product has been discontinued to ensure customer investment security and provide peace of mind.
To ZwickRoell, quality means that we meet all of our customers’ requirements without compromise and regardless of the testing application complexity. We are able to achieve this with our flexible and well designed machines which are developed and manufactured in our own production facilities. This includes mechanical, electronic and software components as well as a wide range of accessories. By adopting this approach we are able to perfectly match our components to each other and meet our own quality standards, allowing us to provide the highest level of product quality and customer support.
What excites you in the industry?
Our company history dates back more than 160 years and we pride ourselves in embracing continuous innovation to drive forward our product development and maintain excellent customer support.
Advances in materials and component testing are focused on the ease with which the associated testing equipment is used, how efficiently the testing procedure can be performed, how we can guarantee repeatable and reproducible test results and whether the introduction of some degree of test automation can eliminate any potential operator error or achieve cost saving via increased testing throughput. ZwickRoell recognises these challenges and strives to ensure that we can offer the optimum testing solution to satisfy any given situation.
New and more exotic materials are being developed to meet a range of ambitions including lightweighting, improved ‘in-service’ performance and cost saving. The need to satisfy ever changing testing procedures means that there is always a requirement to investigate and implement appropriate testing methodologies across a wide range of industry sectors and to bring these solutions to market.
What do you think will be the biggest difference 10 years from now?
There is a view that mechanical testing can sometimes be considered unnecessary, costly and overly time consuming in today’s world of computer modelling and simulation. To reduce costs, some companies may reduce the amount of time and money spent on testing procedures. However, unpredicted materials and component failures when products go into service, can have far worse cost and time implications, including irreparable damage to a company reputation. Product verification via mechanical testing plays a vital role in the design and development process in order to establish ‘fitness-for-purpose.’
Key benefits of physical testing include characterisation of material properties, confirmation that products will work, validation of computer simulations, collection of empirical data to refine and improve simulations, proof of product improvement and visible evidence to customers of product integrity. The impact of witnessing a material or component being mechanically tested under ‘in-service’ conditions rather than in a simulation, cannot be over estimated.
ZwickRoell provides a range of mechanical testing products for metallic and non-metallic materials to ensure products are cost-effective and technologically advanced as well as remaining safe and ‘fit-for-purpose‘ throughout their lifecycle. The future of mechanical testing may see a move towards test specimen miniaturisation, testing in environments which more closely resemble service conditions and the greater use of automation, but the fundamental hardness, impact, tensile, fatigue and creep testing principles look unlikely to change significantly over the next 10 years.
What are the biggest disruptors in the sector?
The materials testing machine sector is a mature market but equipment users are always ready to embrace innovative technologies which provide technical advantage in combination with improved efficiency. ZwickRoell invests heavily in equipment development to maintain our position as a leading brand and product innovator, whilst striving to understand and satisfy the changing needs of our customers across a wide range of testing disciplines and applications.